Historic Building Assessments and Services
Our assessment services for historical buildings are grounded in a multidisciplinary approach, tailored to restore and preserve the integrity of these unique structures. We apply the appropriate engineering and architectural disciplines necessary to assess historical buildings, ensuring they meet modern standards while respecting their historical significance.
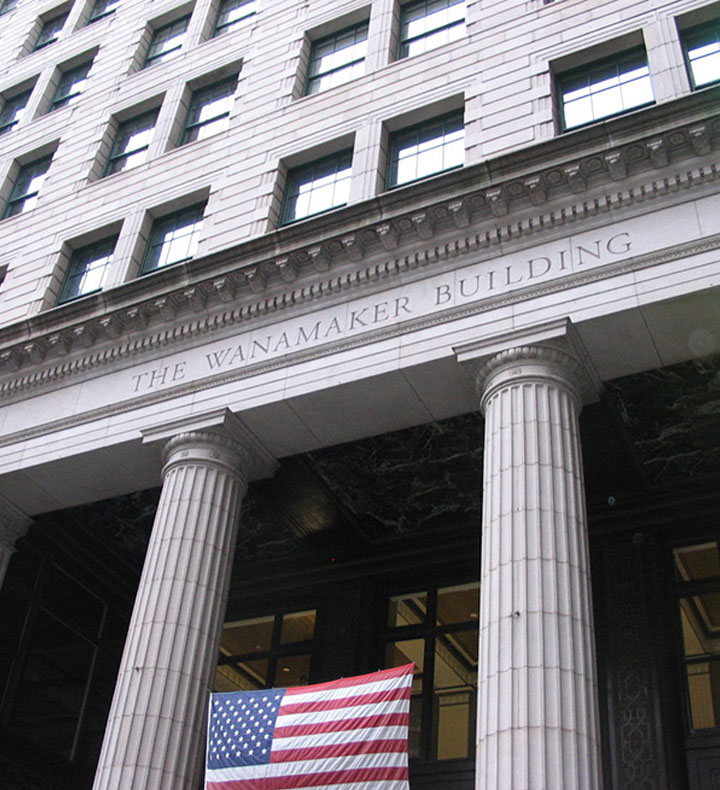
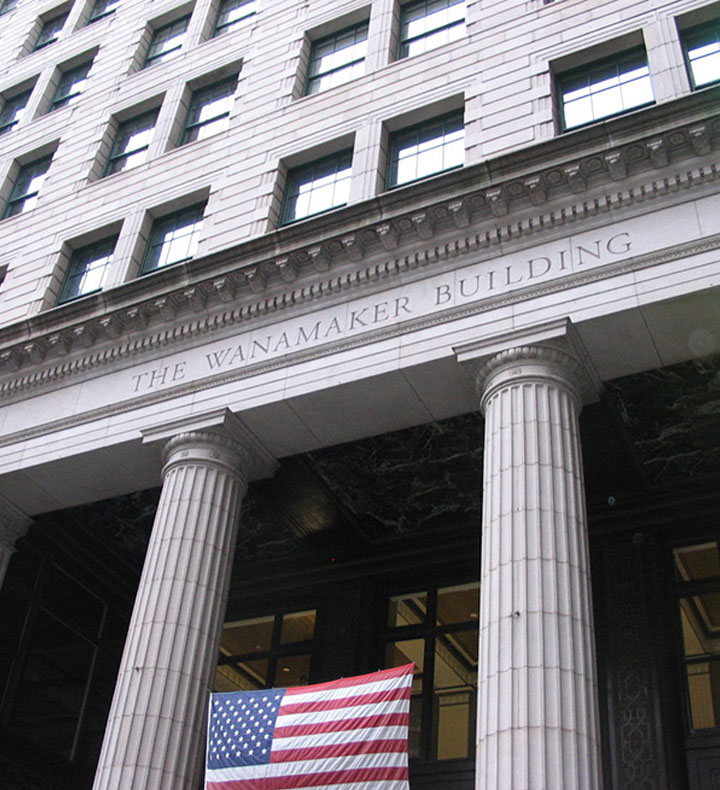
Historic Building Assessments and Services
Our assessment services for historical buildings are grounded in a multidisciplinary approach, tailored to restore and preserve the integrity of these unique structures. We apply the appropriate engineering and architectural disciplines necessary to assess historical buildings, ensuring they meet modern standards while respecting their historical significance.
Property Types
Our approach is versatile and can be applied to a wide range of facility types, including industrial facilities, office buildings, hospitals, college and university buildings, parking structures, and many other types of properties. We understand that historical buildings often require specialized attention to address the challenges posed by aging infrastructure, outdated systems, and the need for modern functionality.
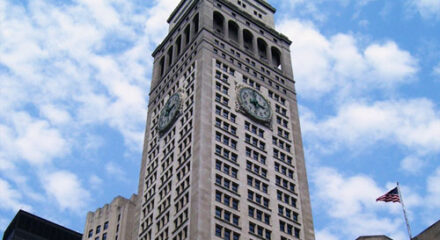
Office Buildings
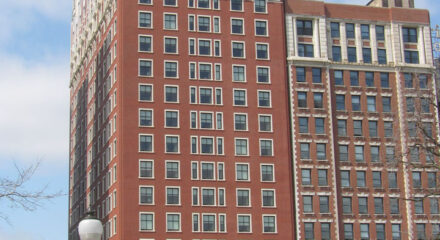
Hotels & Hospitality Facilities

Retail & Mixed-Use

Medical and Healthcare Buildings
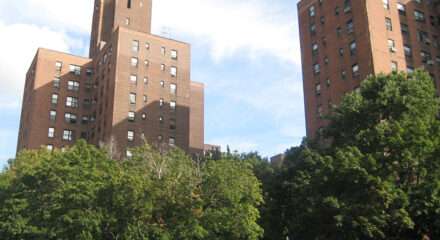
Multifamily Residential
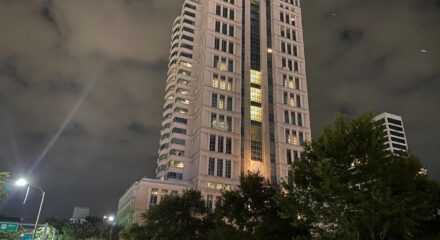
Government & Community Facilities
Our Services
Property Condition Assessments by experienced professionals with a broad knowledge of all building systems. Our assessments are defined by:
- Timely execution for due diligence schedules.
- Thorough field engineering and document analysis.
- Detailed and reliable opinions of cost.
- Comprehensive reporting and photographs.
Development consulting services rooted in engineering & architectural principles; with services span the project lifecycle:
- Site & Development Feasibility Analysis
- Comprehensive Document and Design Review.
- Construction Monitoring, Oversight, and Draw Review.
- Close-Out Reporting and Warranty Inspections
Engineering and construction services for owned assets:
- Capital Projects & Planning Assessments
- Tenant Improvements & Obligation Review
- Emergency Repairs & Insurance Claim Oversight
- Sustainability, Resilience & Building Optimization projects.
Seasoned engineers and architects with experience addressing unique challenges and specialized building systems and an institutional network of established specialty subconsultants for every building system and assessment type.
- Assessments for all building systems.
- Actionable recommendations.
- Extensive and high quality specialist network.
Sustainability, risk, and resilience assessments integrated with our development consulting, asset management, and property condition assessment services. This approach enables stakeholders to explore sustainable and risk-adverse initiatives during investment evaluations and during capital project assessments. This includes:
- Sustainability and efficiency assessments for acquisitions, developments, and owned assets.
- Climate Risk & Resilience assessments for asset managers, risk managers and ESG+R leadership.
Who We Serve
Institutional & Private Equity Investors
Pension funds, insurance companies, or private equity firms, that invest in historic properties.
Lenders & Banks
Lenders and banks that provide financing for office acquisitions, redevelopment, or renovations, offering loans for historic properties.
Developers
Plans, finances, and oversees the construction or redevelopment of historic properties, ensuring design, construction, and operational goals align with market demands and profitability.
Facility and Real Estate Property Managers
Teams that manage the day-to-day operations of a property, including tenant services, staff management, maintenance, and marketing.
Public Entities and Community Organizations
Trusts, foundations, and public organiziations who manage real estate and historically significant facilities.
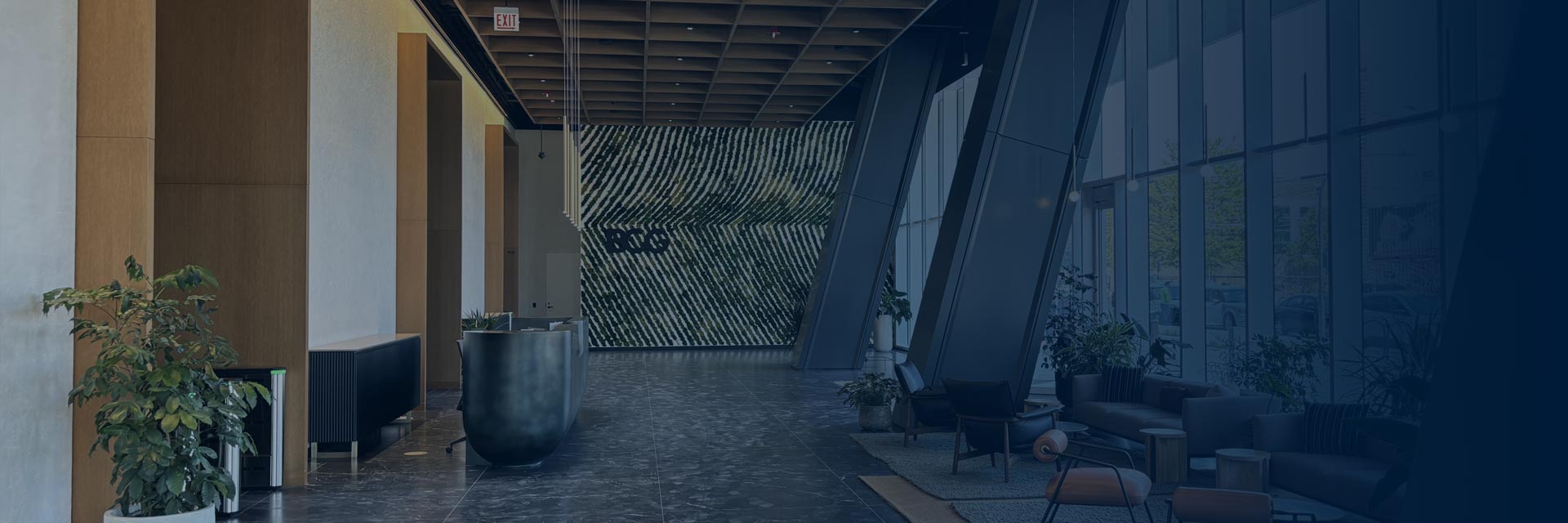
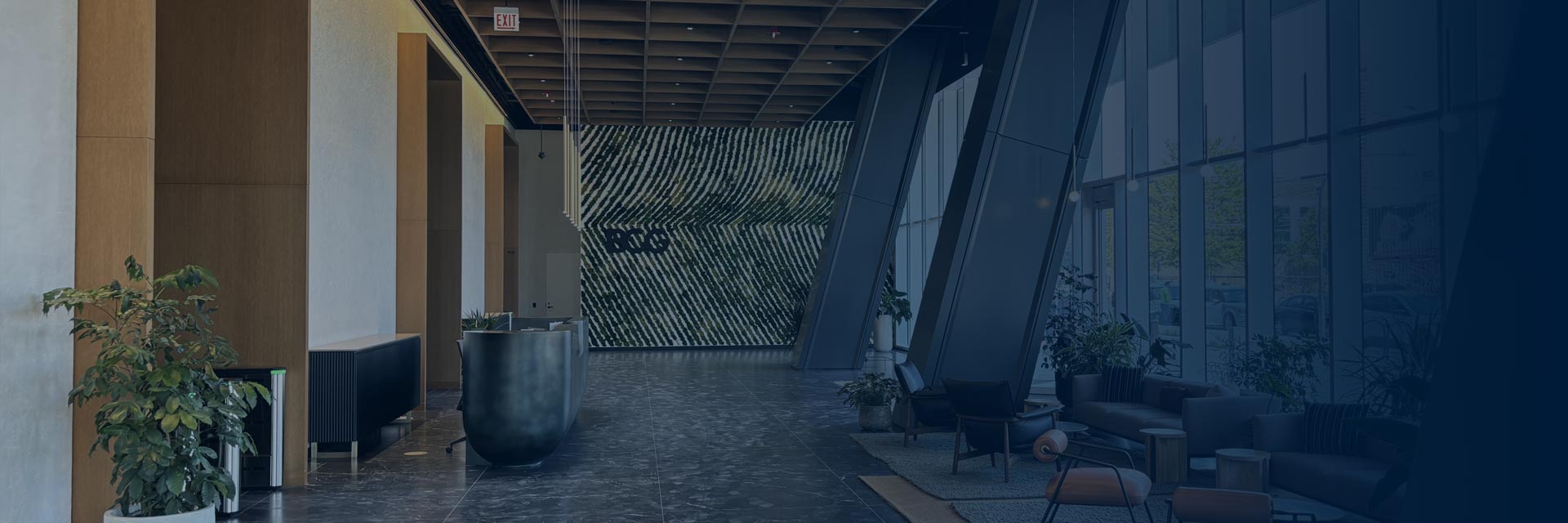